Production process of wax printing fabrics
JI Jun-ling. DAI Ping
Abstract:In wax printing, processeses of pretreatment, wax printing, dyeing, dewaxing, cover printing. Steaming and washing
Are introduced. Factors that affect product qualities are discussed.
Keywords:wax resist printing;technological process;cotton fabric
Pure cotton wax printing products are popular among people in many African countries for their excellent three-dimensionality, rough pattern and rich color [1-2] . The hair wax flower cloth is a novel type in the real wax flower cloth, which is characterized in that the entire main pattern, especially the pattern of the side, the tip, the curved line and the like, emits a flowing silky wax pattern, which is unusually novel and consumers. I can’t put it down. However, the starting wax pattern cannot be produced by conventional crepe lines, special embossing machines, and the like.
Based on the characteristics of the production technology of hair wax, this paper discusses the influencing factors in the production process, and obtains the excellent hair wax fabric by controlling the process parameters of the processing.
1 hair wax flower cloth production process
1.1 Fabric Specifications
137cm, 14.8tex × 14.8tex, 378 10cm × 378 / 10cm cotton poplin
1.2 Process flow grey cloth → tumbling → singeing → rolling liquid stacking → one bath boiling → silk light → white printing wax → main pattern dyeing and hair wax generation → wax removal → parquet rolling → reactive dye Purchasing → steamed water washing → tenter finishing
1.3 production process
1.3.1 Singeing and rolling liquids are piled up in the brush box to facilitate singeing; the smoldering smoldering is two positive and two reverse, the speed is 110m/min, and the singeing level is up to 4, to prevent the cilia and wax from affecting the wax film. crack.
After singeing, the heap liquid is immersed in time. The washing liquid is used as a washing liquid for re-use after boiling, and is provided by a sewage pump through sedimentation and filtration, which contains residual alkali 10g/L and high-efficiency scouring agent KRD. 1 and hydrogen peroxide stabilizer KRD-3. The rolling rate is controlled at 150%. After rolling, the bins are stacked with the cover number for 24h. The rolling liquid is stacked to fully puff the slurry and the impurities in the cotton, and to complex the metal ions, thereby reducing the burden of boiling and bleaching in one bath.
1.3.2 One bath boiling and bleaching prescription / (g·L -1 )
Caustic soda 20
Hydrogen peroxide l0
Hansi@stabilizer KRD-3 5
Hansi@精精剂KRD-18
Multi-dip one-rolling, rolling rate l10%, speed 75m/min, stacking, capacity 6000m, steaming temperature 98~101°C. The first two grids are washed with recycled water, and then washed with water, fully washed out the pulp that is puffed during stacking and easily washed away impurities, reducing the burden of boiling and bleaching, and reducing production costs. After cooking and rinsing, the three grids of hot water are washed backwards, one cold water is cleaned, and the waste liquid is recycled. The three-roll rolling mill has a water content of 70%, wet cloth, and does not need to be dried.
The concentration of caustic soda in the three mercerizing grooves is 180-200g/L, plus Hansi@ high-efficiency alkali-resistant penetrant R-AH 5g/L, the speed is 80-85m/min, 5 strokes and 5 suctions, fully washed, and the alkali is removed in time. Alkali is recycled, no need to distillate, and the pH of the cloth is controlled to be 8.
1.3.4 White roll Before the roll, the pre-treatment quality should be checked. The whiteness is 85, the hair effect is 14cm/30min, and the mercerizing value is 135~140.
The width of the tenter winder should be consistent and the door width should be neat. Place it to bring it back to full moisture.
1.3.5 Printing wax Printing on a copper roller printing machine with a suitable wax.
Printing wax temperature / ° C130
Steam pressure / (kg · cm -2 ) 2.2 - 2.5
Speed ​​/ (m · min -1 ) 60
Active pressure roller pressure / (kg · cm -2 ) 2
Control the scraper pressure spring to make the wax liquid on the surface of the printing wax roll dry and prevent the scraping of the scraping mark; control the opposite side of the printing wax to keep the flower uniform, and prevent the printing wax from being misplaced and printed. Timely water cooling (drinking Indian blue requires cooling of the refrigerator), wet cloth 1000m bin, each box is stacked with wooden mats to prevent creases. In time, tear off the cloth and beat the hand, check the shape and overall effect of the hairline after removing the wax, and adjust the corresponding process parameters.
The printed copper roller has a concave depth of 35-40 filaments, and the concave side of the flower should be vertical. It can be corroded by hydrogen peroxide and hydrochloric acid. In this way, the imprinted wax can be prevented from being extravasated from the edge, causing dyeing to infiltrate the edge and oil outside, thereby producing fine blocks, lines, sharps and curves to ensure the quality of the hair wax.
1.3.6 Main pattern dyeing and hair waxing pattern The main pattern color of the real wax cloth is generally divided into three types: indigo, nafto and indian blue.
When the indigo dyeing machine is assembled, the wind-permeable scaffolding should be permeable. The process flow is: padding indigo reduction bath → padding oxidizing solution oxidation (rotation 4 times) → two-fold water washing → falling cloth de-wax.
(1) Dyeing prescription / (g·L -1 )
Indigo powder l0
100% caustic soda 12
85% insurance powder 25
Hansi@ Leveling Agent DL 3
(2) Oxidation prescription / (g·L -1 )
Hydrogen peroxide 4
Hansi@stabilizer KRD-3 2
pH (caustic soda adjustment) 11
Roll hardness / A. 65
Rolling pressure / (kg·cm -2 ) 1.5
Speed ​​/ (m·min -1 ) 40
The first indigo rolling groove is diluted 20%, the dyeing solution is added, the caustic soda and the amount of insurance powder are tested, and the supplement is added in time; and the wax is removed from the cloth head to see the hand-made pattern, and the effect of the hairline is observed.
1.3.7 Dewaxing The wax is washed by the hot alkali rope-like washing method, and the cloth and the wax infiltrated into the fiber are all washed away to prevent the poor penetration and the yin and yang surface defects during the follow-up printing. When you drop the cloth, you need to pull out the hole and perform the operations of proofing the cloth head, assembling the head and dividing the cloth. For various dewaxing waters, it is necessary to use levitation and floatation, wax and water separation [3] , acid extraction and wax removal techniques to recover rosin, so as to achieve energy saving and emission reduction and cost reduction.
1.3.8 Parquet and dyeing, the dyed fabric after dewaxing, according to the order and the flower number, and pull out the mosaic head, according to the flower back to splicing neatly, to prevent leakage, misconnection, and negligence When printing the trace, the prints such as wrong flowers and latitudes are produced. The roll is made into a neat and dry flower roll using a tenter for printing. If there is a ground color requirement in the order, it needs to be creased and dried, and then the base color is rolled, and then steamed and fixed together with the printing.
1.3.9 Tracking Printing Tracking printing is carried out by reactive dye printing at the printing wax and the main pattern. According to the order and customer sample style and spirit, you can print block flowers, real bubble (sodium sulfite anti-print KN type), wax bubble flower (Indian blue main color with white block imprint, indigo, nafto Citric acid anti-), fake bubble flower (reserved on nickel net), three-dimensional bubble flower (dilute anti-paste or thin white pulp) or as a fake bubble, but the same color paste is used for the round-line chasing and printing on the inner edge. It can print qualified colors and protect hair wax.
1.3.10 steamed water washing Because African flower cloth is dark, rich and colorful, reactive dyes need to use anti-reduction or acid pulp to prevent various bubbles. It is necessary to strengthen the steaming after printing and to enhance the exhaust gas extraction during steaming.
(1) Steaming conditions Fully humidify, strengthen the exhaust gas, the temperature is 103~106 °C, the steaming time is 8 min, and the water is washed after steaming.
(2) Washing conditions: two cold water dilute → two grid soap (temperature 95 ° C, Hans detergent 5 g / L, Hans Baidi anti-sticking agent 2g / L) → two grid hot water wash (80 ° C), two grids Wash with water → press the water to the car to a moisture content of 70% → dry the cloth.
1.3.11 Stretching finishing The coloring wax fabric can be generally soft, sizing and weight-increasing, and can also be calendered.
Process prescription / (g·L -1 )
Hansi@softener WS 10
Starch 20
Hansi@weighting agent CZ 20
Rolling pressure / (kg·cm -2 ) 2
Speed ​​/ (m·min -1 ) 65
Rolling rate /% 100
Temperature / °C 160
Dry the cloth and pull it to the specified width.
2 factors affecting the quality of hair wax
2.1 Pre-treatment white roll quality The pre-treatment white roll quality is shown in Table 1.
Table 1 pre-treatment white roll quality

The requirements for pre-treatment of white rolls are as follows:
(1) After the wax is removed, the white background is white and the waxy wax pattern is clearly visible;
(2) The singeing level is high to prevent the cilia and the wax from being combined into a mesh to prevent the wax film from cracking;
(3) The warp and weft shrinkage rate is small, which can ensure the base fabric is not deformed when the high temperature is printed, and can prevent the wrong printing of the printing process due to shrinkage;
(4) The effect of hairiness and mercerizing value should ensure that the color of the reduction printing process is rich, and the white volume contains uniform moisture. When the wax is printed at high temperature, sufficient moisture is vaporized to break the wax film, so that the crack of the wax film is hard to detect by the naked eye. Cracks form a hair wax pattern.
2.2 printing wax
2.2.1 Depth of the flower tube Table 2
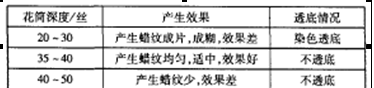
It can be seen from Table 2 that the corrosion depth of the flower tube, that is, the depth of the flower concave, is closely related to the thickness of the wax film printed on the cloth. The flower is too shallow, the wax film is thin, the dyeing is penetrated through the bottom, the wax pattern is formed into a piece, and the paste is formed into a paste; the flower is too concave, the wax film is thick, the dyeing liquid is more, the wax pattern is less, and the effect is poor. After testing, the flower recess is deeply corroded to 35-40 filaments.
2.2.2 Temperature of the flower tube The flower tube is made of seamless steel tube with a circumference of 410 mm and a wall thickness of 12 to 15 mm, with a hollow steel shaft. A steam heating tube is passed through the shaft for printing wax.
Table 3 Effect of tube temperature on printing effect
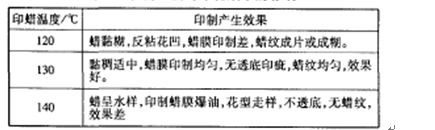
It can be seen from Table 3 that when the temperature of the flower cylinder is 40 to 45 ° C higher than the softening temperature of the wax, the wax pattern is best. The temperature is too low, the printing is difficult, the wax pattern is formed into a sheet or a paste, and the bottom effect is poor; when the temperature is too high, the wax is watery, oil-exposed, no grain, the pattern is out of shape, the steam pressure is large, and the effect is poor.
2.2.3 Wax The wax for the wax wax pattern only needs to add some modifier in the recycled wax.
Table 4 Adjustment formula for printed wax
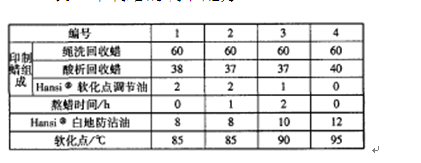
Table 5 Wax quality under different printed wax formulations
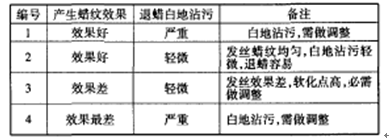
It can be seen from Table 4 and Table 5 that an appropriate amount of Hansi@softening point regulating oil and Hansi@白地防油 are added to adjust and recover the wax liquid composed of rosin, without adding new rosin. The addition of Hansi@softening point conditioning oil and Hansi@白地防油 reduces the waxing time from the original 10-12h to 8h and reduces the softening point of the wax to 82-86 °C. The wax pattern produced at this time is even and beautiful. After the wax is removed, only white stains are slightly stained. In the subsequent reactive dye printing, the conventional reactive dye can be used to print deep, rich and brilliant colors.
3 Conclusion The production of silk wax fabric must be strengthened, strict control of process parameters, such as temperature and pressure of printing wax, including the formation process of hair wax and wax removal, steaming water washing process, etc., to produce flower patterns A pattern of novelty and richly colored wax fabrics. ∞
references:
[1] Zhang Ling. Discussion on the production process of pure cotton wax printing cloth [J]. Dyeing and Finishing Technology, 2007, 29 (11): 17-20.
[2] Ren Jianghong. True wax anti-printing process [J]. Printing and dyeing, 2010, 36 (3): 30-33.
[3] Ren Jianghong, Zhang Deying. Waste wax recovery and wastewater treatment of true wax printing [J]. Printing and dyeing, 2010.36 (7): 3O-32.
When there is liquid in the Pipette tip, do not place the pipette horizontally or upside down, so as to prevent the liquid from flowing back and corroding the piston spring.In the process of biological experiments, especially in the field of Cell Culture, the pipette is an indispensable laboratory instrument, and the pipette holder is also used very frequently on the laboratory ultra-clean bench or in the biological safety cabinet. The ease of use of the pipette and the pipette holder also affects the ease of experimental operation.
pipette drying rack,pipette stand for lab,pipette stand for sale,pipette holder for use,rack for pipette
Yong Yue Medical Technology(Kunshan) Co.,Ltd , https://www.yonyuemedicals.com