I. Overview
In order to improve the surface quality of castings in casting production, the most common method is to apply a layer of coating on the surface of the casting. Graphite powder coating has high refractoriness and low price. It can precipitate bright carbon at the pouring temperature and form a protective film on the surface of the coating. It can reduce the wetting ability of molten iron on the mold, prevent the sticking sand defect, and make the casting easy when falling sand. The characteristics of cleaning and so on are the coatings used in the current production of cast iron. However, the graphite paint is dark in color and close to the color of the furan resin sand, and there is a possibility of misjudging the leak coating. Moreover, there will be a lot of dust when the castings are cleaned, which pollutes the environment and endangers health. Many domestic research institutes have also been developing light-colored sintered peeling coatings, but the same formula is not suitable for castings of different sizes. To this end, we have developed a light red cast iron coating. The coating of the coating is sintered by reaction and the shell is lifted on the surface of the casting. When the coating is cleaned, the coating will automatically fall off from the surface of the casting or peel off after a slight tap. The surface of the casting is smooth and flat. The coating has a wide sintering temperature and is suitable for various types of cast iron parts with different wall thicknesses and sizes.
Second, the coating composition, ratio and preparation
Refractory aggregate
Bauxite belongs to silicon-aluminum refractory aggregate, which is obtained from high alumina bauxite ore by calcination at 1300-1500 °C to obtain corundum bauxite clinker. The source is wide and the cost is low. The main mineral composition of bauxite is corundum (α-Al 2 O 3 ) and mullite (βAl 2 O 3 .SiO 2 ). The high temperature linear expansion coefficient is small, the thermal stability is good, and its refractoriness is ≥1770 °C. Bauxite does not form low-melting substances with metal oxides at the pouring temperature, while the molten metal and its oxides have low wettability to bauxite and have good anti-sticking properties. Considering the wettability and refractoriness of aggregates at high temperature and liquid metal, as well as the surface quality of castings and the cost of castings, bauxite is selected as the refractory aggregate. The main components and physical properties are shown in Table 1.
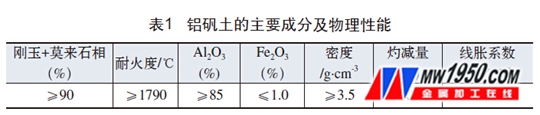
2. Selection of sintering aids
Theoretical studies have shown that if a specific metal oxide is present in the coating, it can promote the expansion of the solid-liquid interval of the coating and the formation of a low-melting mixture during the pouring of the molten metal. These low-melting mixture can well infiltrate the refractory aggregate particles in the coating, and the structure is similar, and it is easy to be melted, infiltrated, crystal phase recombined and the like with the refractory aggregate to form a sintered layer, which hinders further penetration of the molten metal. Since the shrinkage ratio of the sintered layer of the coating material and the metal is large, and the internal stress of the coating is greater than the adhesion to the casting, the sintered layer is easily peeled off.
The coating uses the following three sintering aids.
(1) Iron oxide red is used to compensate for the iron-containing oxide formed by the metal at the pouring temperature, and the consumption of the silicon-aluminum system on the sand surface causes the excess iron-containing oxide to accumulate on the metal surface to a certain thickness and form a peeling. coating.
(2) Potash Feldspar has a melting point of 1200 ° C, which can promote the sintering of high-melting refractory aggregates, and the coating is sintered into a hard and dense molten shell.
(3) The main chemical components of natural zirconium silicate-based minerals are shown in Table 2. The material contains a certain amount of kyanite phase, which can be converted into mullite and cristobalite at a high temperature of 1,100 to 1,650 ° C. The cristobalite is a molten glass polymer at a high temperature, so that the sintering temperature and the melting temperature are relatively high. The characteristics of the wide temperature range. Mullite has a high degree of refractoriness and is stable at 1800 ° C with high chemical inertness. The kyanite phase increases the difference in the linear shrinkage coefficient between the coating and the casting metal, causing a large shear stress on the coating layer and the surface of the casting, resulting in the coating layer peeling off from the surface of the casting. The cristobalite produced during the high-temperature transformation of the kyanite phase is a glass polymer, which can resist the penetration of the molten metal, prevent the mechanical sanding of the casting, and the difference in the linear shrinkage coefficient between the cooled quartz and the casting also promotes the cooling of the coating layer. Peel off on its own.
The above three additives are compounded to make the coating have a wide sintering range, and are suitable for various cast iron parts with different wall thicknesses, different sizes and different pouring temperatures. The compounding ratio of sintering aid is shown in Table 3.
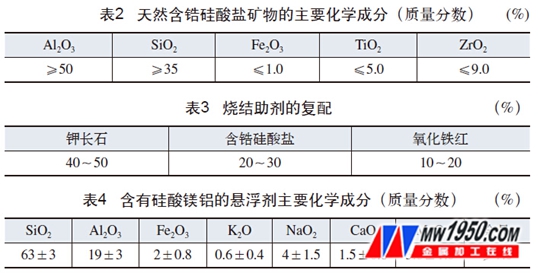
3. Suspending agent
A suspending agent is added to prevent precipitation of the refractory aggregate during storage and use. The addition of a suspending agent gives the coating a certain thixotropy. When the coating is subjected to shearing force during application, the viscosity decreases, and the shear rate increases, and the longer the time, the lower the viscosity. The amount of suspending agent added should take into account the sag and leveling properties of the coating. Typical suspending agents used are lithium-based bentonite, organic bentonite, rectorite, and attapulgite. The amount of lithium bentonite is generally 3% to 6% of refractory aggregates. Because it contains more alkali metals and alkaline earth metals, the refractoriness of the coatings will decrease. Due to the pre-fabrication of water, the water content of the coating is high, and the amount of gas generated during casting is large, which affects the surface quality of the casting. In addition, due to the high water content of the coating, the ignition of the coating is incomplete, and there are many residues on the surface, which affects the surface quality. Lithium bentonite is easy to absorb and swell in water to form a stable colloidal dispersion, but in the alcohol medium, the charged layer is highly compressed, the dispersed particles are aggregated, the colloidal stability is poor, and it is easy to stratify during storage and transportation. The viscosity of the paint decreases, the aggregate settles and agglomerates, and the paint deteriorates.
The amount of organic bentonite is small, about 2% of the refractory aggregate, which does not significantly reduce the refractoriness of the coating, and the gas generation is low, which is beneficial to improve the quality of the casting. However, it requires xylene for its pre-production, and the production and use process will cause harm to people.
Tired stone, attapulgite, etc. also need to be pre-formed with water, so there are also the same problems as lithium bentonite.
After screening, a white composite colloidal substance containing magnesium silicate was used as a suspending agent, and the main components thereof are shown in Table 4.
The suspending agent is non-toxic, tasteless, insoluble in water, and can be directly dispersed in an alcohol-based coating for dispersion. It has a unique three-dimensional space chain structure and a special needle-like crystal structure, and thus has an unusual colloid and adsorption property. It has good stability in the range of pH 3.5~11, excellent thickening and suspension, and the refractoriness is up to 1200 °C. The addition amount is small (usually 0.5%~2.5%), which is very suitable as a suspending agent. coating.
4. Binder
The thermoplastic phenolic resin has strong bonding strength at room temperature, so that the coating can obtain high surface strength at room temperature, but the gas generation amount is large. When the coating amount is large, the coating is easy to crack when it is ignited, causing the pores of the casting; the rosin is not easily cracked after ignition, and the casting surface is cast. Smooth, but its thermal stability is poor, and the bonding strength is low. Therefore, the combination of these two resins can improve the overall strength of the coating, prevent the coating from cracking and cracking, and avoid the occurrence of porosity defects.
5. Other components
The coating is an alcohol base. Considering the low price of ethanol, low toxicity, and strong volatility, industrial alcohol (ethanol content of not less than 95%) is used as a carrier liquid, and an appropriate amount of nonionic surfactant is added to improve the coating. Permeability.
6. Matching ratio
On the basis of refractory aggregate bauxite as the main material, sintering aid was added to investigate the properties of coating suspension, coating, leveling, anti-flowing, surface strength and gas generation, and orthogonal test was adopted. The optimum ratio of the coating was determined, see Table 5.
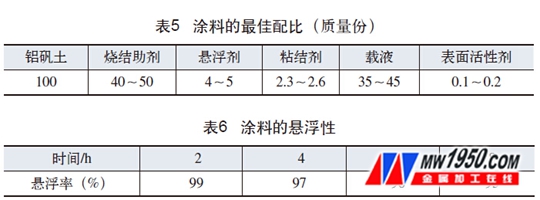
7. Preparation
The phenolic resin and rosin were dissolved in advance at 15% of the total amount of the carrier liquid, and allowed to stand still. Preparation process: 80% of the total carrier liquid + suspending agent → high speed mixer stirring for 20 min → adding phenolic resin and rosin solution + surfactant → stirring for 10 min → adding bauxite + sintering aid → stirring for 30 min → adding total carrier liquid 5% → stir for 15 min, adjust the density → discharge.
Third, the coating performance test
According to the JB/T9226-2008 standard for sand casting, the properties such as density, suspension and viscosity are tested.
(1) Density The density of the coating was measured to be 1.8 g/cm 3 .
(2) Suspension The paint was evenly stirred, poured into a 100 mL stopper cylinder, added to a 100 mL mark line, allowed to stand for 8 hours, and observed for sedimentation every 2 hours. The results are shown in Table 6.
(3) Viscosity According to the standard, the standard -6 viscosity cup is used for 10s.
(4) Gas generation amount Using an SFL recording type gas emission meter, the amount of gas generated at 1000 ° C was measured to be 18 mL/g.
(5) High temperature crack resistance The paint was brushed onto the sample, dried in a blast drying oven at 150 ° C for 1 h, placed in a muffle furnace at 1200 ° C for 3 min, and the surface of the coating was taken out. No paint or sample was found. Peeling phenomenon, the coating surface is smooth and free of cracks.
Fourth, the application of coatings
The coatings were used on the large and small castings produced by our unit foundry and Beiren Machinery Plant. The cast casting has rotor (material QT600-3, blank weight 90kg, outer diameter 400mm, casting thickness 150mm, casting temperature 1340 °C; side cover (material HT300, blank weight 100kg, outer diameter 500mm, casting average thickness 100mm, Casting temperature 1330 ° C); motor housing (material HT300, blank weight 130kg, external dimensions 400mm × 500mm × 120mm, casting thickness 120mm, casting temperature 1330 ° C); cross head bearing seat (material ductile iron, blank weight 380kg, shape Dimensions 890mm × 550mm × 270mm, the thinnest part of the casting is 100mm, the thickest part of the casting is 250mm, and the casting temperature is 1420°C. The shape and core are made of acid self-hardening furan resin sand, and the cross-bearing bearing castings are shown in Figure 1. Figure 2 and Figure 3.
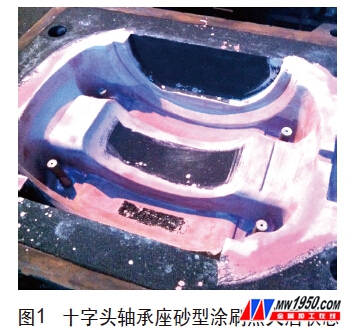
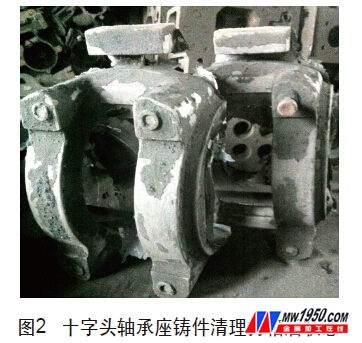
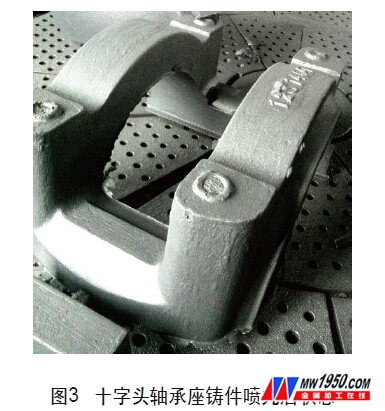
V. Conclusion
The results of production and application show that the paint has good paintability, permeability, leveling, anti-flowing and crack resistance, and the formed coating has high strength. After the shot blasting, the surface of the casting is smooth, without stick sand, pores and clips. Sand defects greatly improve the cleaning efficiency.
About the author: Wang Tongping, Ning Qiangwei, Huang Jifeng, the 12th Research Institute of China Shipbuilding Industry Corporation.
stainless steel, sink strainer,fruit vegetable washing drain basket,kitchen tool,draining rack, draining basket.
Shenzhen Lanejoy Technology Co.,LTD , https://www.brassinsert.net