As we all know, the wall materials used in the previous construction market were mainly red bricks (clay bricks). At present, the state restricts the use of solid clay bricks as filling materials for frame structures in urban construction, and it is forbidden to use solid bricks with strength grade below MU10 in buildings with more than 5 floors. Red bricks have been completely banned in many advanced areas. For example, in the Jiaodong area of ​​Shandong Province, the government has explicitly banned the red brick market and forced the use of lightweight brick equipment. The design unit shall indicate the use of environmentally-friendly lightweight bricks in the process of designing the building. If the red brick is used, the quality inspection department will not accept it. As a result, the light brick market is in short supply, attracting investors to invest in entrepreneurial production.
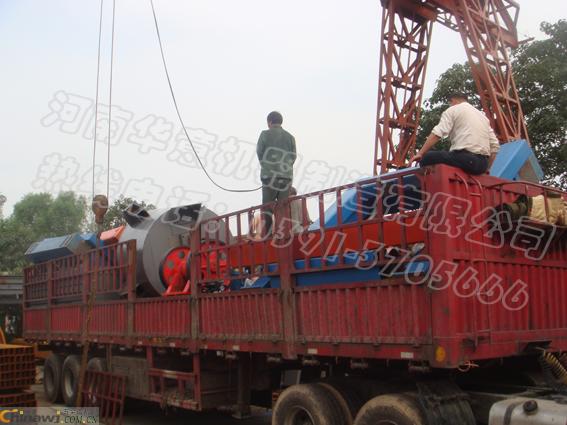
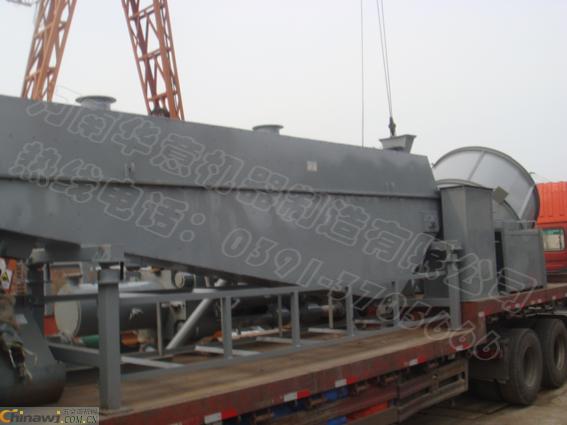
It took a lot of money to introduce advanced lightweight brick equipment into the lightweight brick production line, but it always caused various damages in the production process, which seriously affected the cost benefits and became a headache for many lightweight brick manufacturers. Henan Huayi Machinery Manufacturing Co., Ltd., as a modern high-tech enterprise specializing in the production of lightweight brick equipment, we pay attention to the recognition of customers. The customers think of it and did not think of it. We all do it in advance. Let us tell you by our Huayi technicians. How to prevent various damages in the production process of light brick production lines:
One is before autoclaving and the second is after autoclaving. In the production process of autoclaved lightweight brick blocks, the following conditions are generally slow, and each case can be avoided by mechanical means or operation skills.
1, heart
Sometimes the middle part of the product is darker in color. We call it a heart or a black heart. Even the whole piece has a darker and dull color. This is caused by no steaming. First, check whether the steam meets the requirements. Whether the autoclave curing system is feasible, whether the relevant equipment is in good condition; then check the raw materials and make adjustments.
2, crack
Cracks in the product of the kettle are common damages in the production of light brick equipment. The cause of the crack may be raw materials, or may be autoclaved.
When the strength of the green body is too low, steam curing can also cause damage to the green body. When the autoclave curing system is improper, it may also cause arc cracks in the whole mold body. Other cracks are not caused by autoclaved curing, but can only be found after autoclaving. Among them, water-to-material ratio, pouring temperature, mix ratio, and parking environment of the blank have the greatest impact.
3, adhesion
Adhesion is to indicate that there is a lot of adhesion between the block and the block, which causes a lot of adhesions. However, this phenomenon mainly occurs after autoclaving. The adhesion is actually the cutting crack and the blanks on both sides of the gap are not blocked. In the process, due to the hydrothermal synthesis reaction, the hydration product passes through the material in the gap and extends to the opposite side to crystallize, so that the weights of the separated billets are connected together, and the adhesion element is moisture, and the residual in the gap The ratio of the space occupied by the material, the dissolved amount of sio2 and CaO in the water, and the like. That is to say, the adhesion is related to the moisture in the blank, the width of the cutting joint and the ingredients. Practice has shown that the strength of the green body at the time of blocking and cutting is more closely related to the static temperature of the pouring temperature than the pouring temperature, and the autoclave curing system is closely related. Solve the above relationship and completely solve the problem of adhesion of products.
4, burst
The main effect of the burst is that when the kettle is discharged, the surface of the product is peeled off to form a surface pockmark. The main reason for this is the over-burned lime granules or the agglomerates of the benefits and other materials without even mixing.
The burnt lime particles are not digested during the static stop of the casting, but are rapidly digested under the high temperature conditions after being charged into the kettle, and at the same time, the expansion of the volume causes damage to the product. The disintegration of the lime agglomerates without agitation may have already caused damage to the green body during the static stop or cutting. During the autoclave curing process, the damaged portion is further peeled off from the green body due to the larger expansion value of the lime agglomerates. The agglomerates of other materials also cause damage to the product due to slower water absorption and later expansion.
The bursting may also be due to the poor gas permeability of the green body. The strength of the green body is too low when the kettle is introduced. During the vacuuming process, the pore wall structure cannot withstand the pressure difference between the inside and the outside of the blank; when the pores are not uniform or the aluminum powder degreasing agent is not At that time, it may also cause a burst, but each burst has its own characteristics. Such as lime particles or poor pore structure, we adjust according to different situations.
5, surface pit and collapse
Surface pits and collapses are mostly caused by condensed water in the pipeline. In the past, the inlet pipes of the autoclave were arranged at the top, so that when the intake air warmed up, the condensed water in the pipe directly impacted the above-mentioned blank, thereby forming damage. Now, most autoclaves have been changed to air intake on both sides, but the air holes of the intake pipe should also be avoided to directly face the blank.
6, mucosa
The mucosa is the most common damage in the autoclaving stage of pouring and cutting. It occurs at the same stage, and the reason is roughly the same, that is, the bottom plate is not properly oiled, or the bottom plate is not saturated with oil, or is selected. The viscosity of the oil is too low. When the bottom plate does not have oil absorption, it is easy to be washed away by the slurry during the pouring process. After the pouring is finished, the coating is also easy to penetrate into the green body, which not only destroys the isolation effect, but also reduces the strength of the bottom layer of the green body and easily causes mucosa. Second, some static stop tables are equipped with steam heating pipes. When the steam temperature is too high, the oil layer of the bottom plate is easily infiltrated into the blank body, thereby causing a sticking mold. Thirdly, the bottom plate is not cleaned, the adhesive on the floor forms a firm bond with the recast body, and the bottom plate adhesive is cured by repeated autoclaving, and the adhesion to the floor is also stronger, thereby causing repeated Sticky mold.
Our service is not only recognized by customers, but also pursues customer success, your satisfaction, our hopes; your hopes, our pursuit. Huayi never wants to speak out, as long as the quality and after-sales to fight the world, excellent products, excellent service is the commitment of Huayi people, welcome domestic and foreign merchants to visit and guide!
Let us use your professionalism to achieve your brick industry! Manufacturer recommended equipment: aerated concrete equipment, aerated concrete block equipment
Telephone
Grinding Wheels
Introduction:Has perfect abrasive performance and extra durability on application of steel, obvious advantage among the competition of various brands.
1.6mm thickness can fast cut different material, minimize the friction and increase sharpness.
Used for 6``grinder, 150mm diameter products are suit to Europe, South-America, Middle-east and etc.
grinding wheel cutting disc
. SPECIAL FIBER GLASS NET
Safe, steady, strong side load capacity with good versatility.
DURABILITY
30% performance more than common products,highly improve working efficiency and lower the average cost.
SHARPNESS
Quick and clean cutting with good stability.
BURNING CORROSION
Smooth one step white cutting with the metal, no need further polishing.
STRONG METAL RING, NO DROPS
Small cutting working area,less dust,
no material loss.
Used for medium power angle machines , display the best performance. Used for high stress working, excellent abrasive performance, high stability in grinding pipe Metal grinding disc provides a high burr removal capability of the general types of iron and steel Has perfect abrasive performance and extra durability on application of steel.
The related abrasive products we can supply is Flap Disc Adhesive , Abrasive Sanding Disc, Flap Wheels , Abrasive Flap Disc , and Abrasive Machine such as Flap Disc Making Machine,Abrasive Belt Making Machine, Flap Wheel Machine , Polishing Machine ,Sanding Disc Machine, if you have any needs about abrasive tools, please kindly feel free to contact us.
Grinding Wheels,Polishing Grinding Wheel,inch grinding wheel,Grinding Wheel For Metal,Polishing And Grinding Wheel
Zhengzhou Jiading Abrasive Manufacturing Co.,Ltd , https://www.jd-abrasives.com