According to the fuel, the steam boiler can be divided into an electric steam boiler, a fuel steam boiler, a gas steam boiler, etc.; according to the structure, it can be divided into a vertical steam boiler and a horizontal steam boiler, and the small steam boiler is mostly a single and double return vertical structure, large Steam boilers are mostly three-return horizontal structures.
structure
Vertical double return structure
The vertical fuel gas steam boiler adopts the burner down mode, the second return structure, the fuel combustion is sufficient, the boiler runs stably; the smoke pipe is inserted with the spoiler to slow the smoke exhausting speed, increase the heat exchange amount, the boiler thermal efficiency is high, and the user is reduced. cost.
Horizontal three-return structure
The horizontal steam boiler is a three-way pyrotechnic tube structure with a full-humid back-flow and a back-flow. The flame is burned in a large combustion chamber with slight positive pressure, fully extended, low heat load, high combustion heat efficiency, effectively reducing the exhaust gas temperature and saving energy. Reduce consumption and use the economy. The corrugated furnace and the threaded pipe structure not only improve the heat absorption strength of the boiler, but also meet the needs of the heat transfer surface to be thermally expanded, scientific and reasonable, and durable.
Steam boiler operation method
Before the boiler is pressed, the actual party reduces the boiler load, and then according to the length of the shutdown time, the coal seam is thickened (generally only 200 mm), and the grate speed is appropriately accelerated, when the thickened coal seam is from the old millimeter eagle iron ( When the slag stopper is about 1 mm, stop the grate rotation, stop the drum and the induced draft fan, and adjust the regulating plate block and the flue baffle for the small-section air supply, and rely on natural ventilation to maintain the weak combustion of the coal, and then discharge the sewage. Raise the boiler water level to the highest allowable water level. If the fire burns out the coal sluice plate, the grate can be started again to move the coal to a certain distance after the emergency shutdown of the steam boiler. When the boiler needs to resume operation, as long as the pilot and blower are started, adjust the opening degree of the smoke, wind baffle and sectional wind chamber to adjust the baffle. When the combustion is normal, adjust the thickness of the coal seam and start the grate to resume operation.
Emergency shutdown of steam boiler
(1) First stop the coal supply and air supply, the chain furnace should hang the curved baffle, the coal pulverizer stops the coal throwing, and weakens the wind, and closes the small flue baffle.
(2) Depending on the nature of the accident, some should release coal from the furnace, and some should not let off coal. The method of releasing coal is: the grate should send the coal into the hopper at the highest speed. After burning coal ash hopper, water can be used to smear or use sand. The ash of the wet furnace is pressed on the coal to extinguish the fire. However, under no circumstances should water be poured into the furnace to cool the boiler.
(3) After the steam boiler is extinguished, the main steam valve should be closed to isolate the main steam pipe from the steam main pipe and close the induced draft fan. To make the nature of the accident, if necessary, open the air valve, safety valve and superheater trap to quickly discharge steam and reduce pressure.
(4) Turn on the provincial gas bypass flue, close the main road flue, and open the large flue baffle, ash door and furnace door to promote air dredging and increase the cooling rate.
(5) In the case of emergency shutdown, there is no shortage of water and full water. Water supply and sewage can be used to accelerate cooling and reduce boiler pressure. When the water temperature drops below 70oC, the pot water can be drained.
(6) If the boiler is urgently shut down due to lack of water in the boiler, it is strictly forbidden to supply water to the boiler, and it is also impossible to open the air valve or lift the safety valve to adjust the exhaust gas to prevent the boiler from being subjected to sudden temperature or pressure changes. expand.
(7) When it is determined that the boiler is full of water accidents, stop the water supply immediately, turn off the small ventilation and flue baffles, reduce the combustion, and open the drain valve to release the water, so that the water level is properly lowered; at the same time, open the main steam pipe, superheater The steam main pipe and the hydrophobic door on the sub-cylinder prevent a large amount of steam from carrying water and water shock in the pipe.
Steam boiler daily operation and maintenance
Because the boiler is a special equipment, in order to ensure its normal operation, to avoid accidents, maintain the normal service life of the boiler.
The daily operation of the boiler should be strictly in accordance with the following requirements:
1. The personnel of the boilers who are certified by the boilers must obtain the certificate of the furnaces issued by the Municipal Bureau of Quality and Technical Supervision (this is required by the quality and technical supervision bureau at the time of acceptance of the boiler).
2. Strengthening water quality management Steam boilers are caused by the continuous evaporation of boiler water, which causes the boiler water concentration to rise and scale. In addition, if the boiler water concentration is too high, there will be boiling water boiling phenomenon, which will lead to the occurrence of boiler false water level, which will affect the normal operation of the boiler. It will cause the boiler to dry and the furnace bulge accident. In order to prevent this from happening:
A. Strengthen the management of boiler water treatment equipment: Regularly test the boiler water treatment effluent to ensure that the boiler feed water meets the GB1576 "industrial boiler water quality" standard requirements.
B. Strengthen the management of boiler water: Regularly test the water quality in the boiler to ensure that the water quality of the boiler meets the requirements of GB1576 “Industrial Boiler Water Qualityâ€, and timely discharge of water and slag.
3. The daily use of the water level gauge should be kept clean, avoiding the pollution and affecting the observation of the water level and the accumulation of scale in the water connection pipe, and the false water level phenomenon in the Dussels will cause the boiler accident to occur. A flush check should be performed once a day for this purpose. The rinsing method (under the boiler at 0.1-0.2 MPa) is as follows:
1. Open the drain valve of the water level gauge so that the steam connection pipe, the water connection pipe and the water level gauge itself are flushed by steam and water;
2. Close the water connection pipe so that the steam connection pipe and the water level gauge itself are flushed by steam;
3. Open the water connection pipe valve, close the steam connection pipe valve, and make the water connection pipe flush with water.
4. Open the steam pipe valve, close the drain valve, and finish the flushing operation to restore the normal operation of the water level gauge.
4. Daily Sewage Operation Because scale slag and the like may cause the sluice of the sewage disposal device, it is necessary to perform at least one discharge every day to maintain its normal operation. Sewage discharge method: Before the sewage discharge, the water level of the boiler is at a normal high water level, and the boiler pressure is carried out at 0.1-0.2 MPa. The principle of “diligent discharge, less discharge, uniform discharge†(at least once a day) is short and intermittent, that is, the sewage valve is opened. After the off, close and then open, so repeated several times, until the water level is at a normal low water level. Remember not to empty the boiler.
5, daily maintenance In order to prevent the air from causing corrosion to the boiler and affect the normal service life of the boiler, the furnace should be shut down and started according to the following methods:
A. When the furnace is shut down, the power should be shut down under normal pressure and the main steam valve and the boiler inlet valve should be closed in time to prevent air from entering the boiler.
B. First open the boiler inlet valve when starting the furnace, turn on the total power supply of the boiler and open the main steam valve to increase the exhaust pressure. When the pressure reaches 0.1-0.15Mpa, close the valve to boost, and then press the pressure to normal working pressure. The valve is supplied with air.
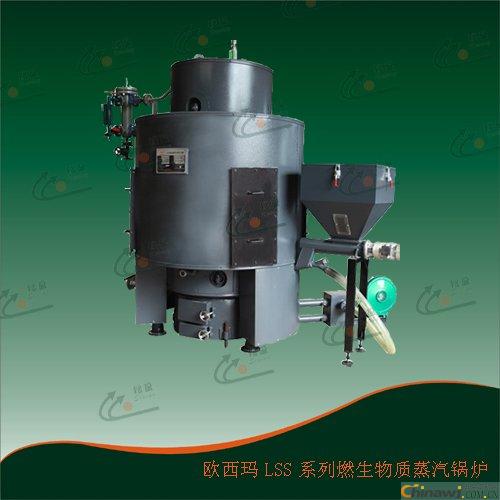
Vials Filling Peristaltic Pump
The working principle of a Vials Filling Peristaltic Pump is like a snake swallowing an egg. The hose is constantly squeezed through the roller to make the hose generate pressure and push the liquid forward. Our designers make the Peristaltic pump head and hose fit perfectly by designing precise roller size and pump head structure. So as to achieve the purpose of accurate liquid metering transmission or filling. The Vials Filling Peristaltic Pump motor uses a high-precision stepping motor with precise operating speed and angle, combined with the interactive interface carefully designed by our electronic engineers for customers, so that customers can achieve reliable liquid quantitative transmission or filling through simple operating steps.
Suitable for various vials filling applications.
Vials Filling Peristaltic Pump,Electronic Cigarette Pump,Peristaltic Filling Pump,Food Grade Peristaltic Pump
Baoding Chuangrui Precision Pump Co., Ltd. , https://www.crprecisionpumps.com