The ISO S classification of workpiece materials includes high temperature alloys (HRSA) and titanium alloys. The thermal hardness and thermal strength of these materials make them widely used in critical applications in aerospace, energy and other fields. However, the beneficial properties of these alloys also bring about processing characteristics that are different from traditional steel processing. To address this issue, tool manufacturers have developed a range of product and application strategies to address material processability challenges and achieve reliable, stable and relatively economical ISO S material combination gold processing. Today, these toolmakers are also striving to provide manufacturers with training on new tools and strategies, and to persuade machine toolmakers to rethink outdated processing techniques that are likely to be unsuitable for today's advanced materials. Processability Factors The term "processability" describes the reaction of a metal to a processing process. Machinability includes four basic factors: mechanical forces generated during machining, chip formation and chip removal, heat generation and transfer, and tool wear and failure. Excessive effects of any or all of these factors can cause materials to be considered "difficult to process."
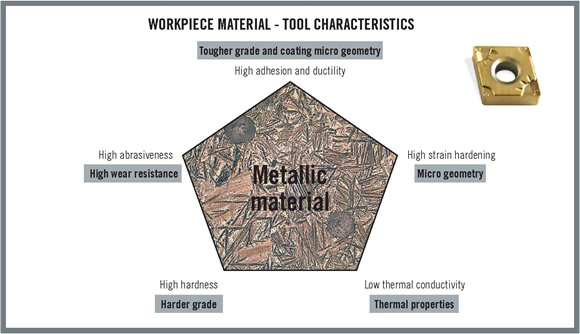
If you try to use the same tools and techniques used for materials such as steel over the past few decades for high-temperature alloys and titanium alloys, it can cause problems in tool life, machining time and reliability, and part quality. In recent years, nickel-based alloys and titanium-based alloys have been considered in the development of tools. Processing these relatively new materials is not necessarily more difficult than processing traditional metals, which is actually two different types of processing.
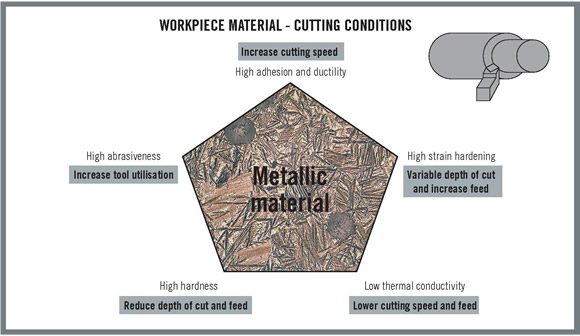
For example, the usual method of machining "difficult to machine" materials is to operate with care and use lower cutting parameters, including reduced feed rates, depth of cut, and speed. However, when using tools developed specifically for these high-performance workpiece materials, the basic principle is to increase the depth of cut and feed rate. Tools designed to handle these higher parameters contain fine-grained carbide grades that provide good high-temperature edge strength and coating adhesion, with special attention to groove wear resistance to work hardened workpieces. In addition, tool manufacturers have developed ceramic and PCBN tools for roughing and finishing these high performance alloys.
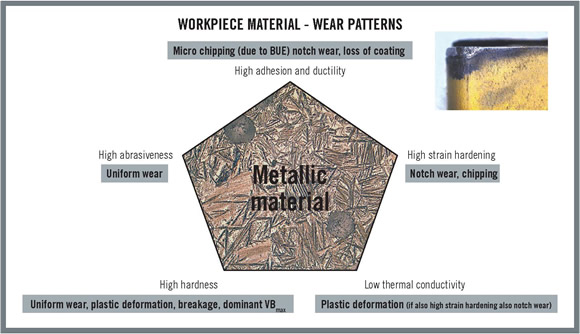
For certain processability factors, superalloys do not differ much from tough steel materials in terms of mechanical or force-related problems. However, there are significant differences between heat generation and heat dissipation. The heat generated during the metal cutting process causes the workpiece material to deform, and the chips generated during the cutting process can remove heat. However, the segmented chips produced by these materials often do not provide good heat dissipation. In addition, the heat resistant material itself is a poor thermal conductor. The temperature in the cutting zone can reach 1100° - 1300° C. When the heat cannot be dissipated, it will accumulate on the tool and the workpiece, and eventually the tool life will be shortened, and even the deformation and metallurgical properties of the workpiece will be changed.
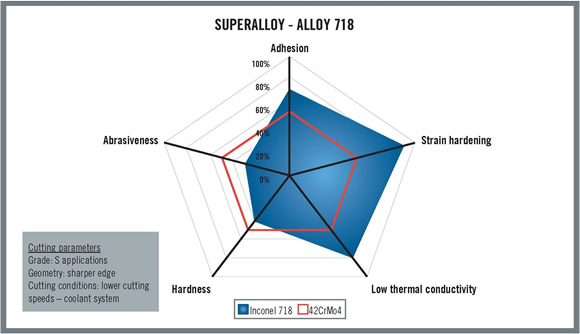
To solve this problem, you need to change the understanding of the tool strength. Tools with sharp edges are generally considered to be fragile, but one of the ways to control the temperature build-up of the tool is to use sharp tools that cut more material and reduce material distortion, thus generating less heat. Implementing this strategy requires a tool designed for the strength of the cutting edge and is used on machines with sufficient power, stability and vibration resistance.
The trend of strain hardening and precipitation hardening also increases the complexity of high temperature alloy processing. In strain hardening, the material in the cutting zone becomes harder when subjected to stress and high temperature during the cutting process. Nickel-based and titanium-based alloys exhibit a greater strain hardening tendency than steel. In precipitation hardening, when high temperature activates an alloying element that should be at rest, a hard spot is formed in the workpiece material. Regardless of the trend, the structure of the material may change significantly after the first pass, and will penetrate the harder surface after the second pass. And this is the solution to minimize the number of passes. For example, instead of using a 5 mm cut depth to cut 10 mm of material, it is better to use a 10 mm deep cut. Although in many cases it is not possible to achieve a single pass, it is still a theoretical goal.
This method also requires reconsideration of the finishing process, which involves multiple passes with small depth of cut and light feed rate. As an alternative, machine tool technicians should look for the possibility of maximizing the parameters in order to improve tool life and surface roughness.
The slightly larger depth of cut used to finish the pass can also place the sharpest part of the cutting edge below any strain hardened or precipitation hardened area of ​​the part. However, an excessively deep finishing pass may cause vibration and adversely affect the surface roughness. Therefore, finding the best balance between aggressiveness and caution becomes the key.
Reliability and economy
With the tools and strategies now developed for nickel-based and titanium-based alloys, there is basically no technical problem with the finished machining. The continuing challenge is not only the machining of the workpiece, but also the correct machining of the workpiece at the specified cost within the specified time. The goal is to improve process reliability and production economy.
Considering the high cost of advanced workpiece materials and parts made from them, the machining process must be absolutely reliable. Manufacturers cannot afford to produce lost parts while seeking a reliable process. The use of appropriate tools and machining parameters helps ensure consistent machining results.
In terms of processing parameters, increasing depth of cut and feed rate contribute to productivity. Higher cutting speeds also speed up part machining, but this advantage has not been fully exploited. The speeds currently used in nickel-based and titanium-based alloys are still lower than those in steel. However, the current research focus is on developing tool properties that enable higher cutting speeds while still maintaining a reasonable tool life.
In addition to tools, other components of the metal cutting process, such as the use of high-pressure directional transport coolant (HPDC) systems, help increase productivity. If the ISO S material has a cutting speed of 50 m/min, HPDC can cut up to 200 m/min, resulting in a fourfold increase in throughput.
Tool life is another factor that can be viewed from a new perspective when machining superalloys. The traditional method of calculating tool life is to calculate the number of minutes before the tool needs to be replaced. Another method of measurement is to calculate the cost.
For example, if it takes 2 hours to produce a specific part and the tool must be changed every 20 minutes, you must purchase 6 tools to complete the part. Following this line of thinking, the goal will be to reduce tool costs and get a 30-minute tool life instead of 20 minutes.
However, when machining expensive parts made of superalloys or titanium alloys, the cost of the tool is only a small fraction of the overall value of the part. Therefore, tool utilization (also known as tool utilization index) is a more relevant measure. When comparing two example tools, if one tool is maintained for 10 minutes and
To produce a workpiece, the tool cost is one tool per workpiece. Another tool, used in different ways, may only last for 5 minutes, but produces two parts. Even though the life of the second tool is half the life of the first tool in terms of minutes, the part production is doubled. The goal is to produce the maximum number of qualified parts in the shortest amount of time at an acceptable price. Considering the high cost of high-temperature alloy parts, the tool utilization index is a better measure of real productivity.
in conclusion
As always, the key to maximizing the benefits of newly developed metal cutting technology is to understand how best to apply it to a specific application. With continued advances in high-performance workpiece materials such as superalloys and titanium-based alloys, toolmakers will continue to design new ways to maximize productivity for new alloy processing. Manufacturers will benefit from an understanding of the availability of new tools and the extensive knowledge of tool manufacturers in how to best use them.
Continuous tool development
Stainless steel, patented in various forms about 100 years ago, became the first step towards modern superalloys. In the first stainless steel alloy, chromium is added to the steel for oxidation and corrosion resistance – in basic stainless steel alloys, the chromium content is at least 10.5% of the total weight. Next, in order to improve the hardness and rigidity of the stainless steel, nickel was added. As alloys are used in increasingly harsh environments, the proportion of nickel increases, and eventually nickel becomes the main alloying element in the material. In today's well-known superalloy 718 (trade name Inconel 718), the nickel content is 50% to 55%, the chromium content is 17% to 21%, the other elements are 10%, and the remainder is iron. Modern high temperature alloys and titanium based alloys have excellent strength, heat resistance, corrosion resistance and stability.
In the face of these difficult-to-machine new workpiece materials, manufacturers should first try to use familiar processing practices. However, only when they use the tools and techniques that are specifically designed for these specific materials and processes can they achieve maximum productivity.
For example, in the mid-1980s, Seco set up an “Alpha Group†of scientists and engineers to find more efficient stainless steel processing methods. The team worked with a number of stainless steel manufacturers to develop new carbide grades and geometries, as well as special cutting methods for stainless steel. In the 1990s, they extended their development activities to high-performance superalloy materials.
In addition to carbide grades, coatings and geometries, tools have been developed to optimize superalloy machining productivity during specific stages of the metal cutting process. For example, for high-speed machining operations, Seco's CS100 sialon grades offer excellent chemical stability, corrosion resistance and stiffness for long-lasting, stable tool life. Typical roughing application parameters include cutting speeds from 150 m/min to 305 m/min, feed rates from 0.2 to 0.4 mm/rev, and depths from 0.5 mm to 3.75 mm.
The Secomax CBN170 complements the CS100 grade, a tough and wear-resistant PCBN grade designed for continuous finishing of nickel-base superalloys.
The CBN170 grade contains a whisker ceramic bond that extends tool life and reduces the number of machine downtimes required to replace the cutting edge. This grade is designed to meet the exact surface roughness, tolerances and cutting length requirements of nickel-base superalloy finishing operations. The CBN170 tool is designed for machining in continuous cutting conditions with coolant, cut to depths of up to 0.5 mm and cutting speeds from 300 m/min to 400 m/min. This material grade has a CBN content of 65% of the total volume and has a particle size of 2-?m. The blade has a 25-?m edge grinding specification.
Other developments aimed at improving tool life and productivity in superalloy processing include Seco's Jetstream Tooling High Pressure Directional Conveying Coolant (HPDC) system, which delivers coolant to the vicinity of the cutting edge. The coolant jet removes chips from the rake face, improving chip control and tool life, and enabling higher processing parameters. In some cases, the rapid cooling of the chips makes them brittle and thus more susceptible to breakage.
Headquartered in Fagersta, Sweden, Seco is committed to developing innovative metal cutting solutions and working closely with customers to fully understand and focus on meeting their needs. We employ more than 5,000 people in 50 countries and enhance the capabilities of our team members through training, development and employee recognition programs, and an open communication environment. Our employees demonstrate three core values ​​– enthusiasm, family belonging and personal commitment – ​​which define the way we do business and how we interact with our customers, suppliers and other partners.
Farmhouse Sinks
As one of the most important components of the kitchen, the sink is more than just a basin you use to clean your dishes, it`s often a focal point of the room itself. And being a focal point of the [heart of your home," it`s always a good idea to choose a sink that complements your unique style and decor of your home.
Also known as an apron sink, a farmhouse-style sink features a deep basin and an exposed front that sits flush with your cabinets and countertops. With a touch of country charm, this type of sink offers a number of functional benefits that make it a great choice for many kitchens.
The Pros:
Here are some of the most prevelant benefits you can expect from a farm style sink.
Extra Capacity:
The additional width and depth of these sinks allows plenty of room for soaking dishes, large pots and pans, and other hard-to-clean items, such as grill grates, stock pots, and baking sheets. Because apron sinks are located in a forward orientation relative to the countertops and cabinets, it's also easier to lift heavier items in and out of the sink.
More Versatility:
Typically, a farmhouse sink won`t include pre-drilled holes for a faucet. While this may seem like a bad thing on the surface, this actually provides homeowners with a bit more flexibility in choosing the best faucet for their needs.
In most cases, the faucet will be installed on the countertop directly behind the sink, but this gives you the option to install the faucet wherever works best for your kitchen. Or, perhaps you love the faucet you currently own, and just want to upgrade the sink.
Alluring Appearance:
Let`s be honest here. The "look" of a farmhouse sink is probably one of the driving factors as to why you`re interested in owning one. The extra capacity is just an added convenience. But, there`s no denying that it creates a natural focal point in an area of your home where you spent quite a bit of time.
Lots of Options to Choose From:
As you can see from the list above, farmhouse sinks are available in a wide variety of materials, colors and finishes. This makes it incredibly easy to find one that complements the style of your kitchen, and blend right into the cabinetry and other appliances in this space.
Farmhouse Sinks,Top Mount Farm Sink,Modern Farmhouse Sink,Stainless Farmhouse Sink
Guangdong Huayou Hardware Products Co.,Ltd , https://www.gdhuayouhardware.com